用于小样本下故障检测的跨传感器生成式自监督学习网络
## 论文相关信息
本文内容取自[1]。
本论文的介绍链接
研究意义
设备维护是保证工业制造系统安全、可靠和可用性的重要环节之一。随着自动化技术的飞速发展和实际生产需求的不断提高,机械设备的集成化和复杂程度不断提高,以适应各种复杂恶劣的工况。这一进展对维修复杂系统的维护决策提出了更大的挑战。设备故障或停机可能导致重大的经济损失。因此,尽早发现设备异常状态并进行维护保养,是保证设备安全可靠运行的关键。故障检测对于及时发现设备的异常运行状态起着至关重要的作用。这样就可以进行必要的机器维护以排除故障,加快非计划维护,减少设备停机时间,并最大限度地减少性能下降,以防止严重的安全事故。
同时,由于故障的偶然性,通常很难收集到足够的故障样本,即缺少注释数据。由于样本稀缺,许多研究人员转向自监督学习来克服故障样本不足的挑战。然而,这些方法仍然存在局限性:现有的深度学习方法没有考虑不同传感器数据之间的区别,通过简单的通道拼接来训练多传感器数据可能无法有效提高模型性能。
本文工作
本文提出了一种新的生成式自监督框架,旨在解决已有方法的局限性。特别是,我们深入研究了来自不同传感器的数据之间的区别,并提出了一个基于传感器间重建范式的生成借口任务框架。跨传感器方法可以通过自动编码器实现多传感器数据之间的交互。同时,我们的多传感器方法协调特征融合,在时间维度内从粗粒度表示过渡到细粒度表示。在整个预训练阶段,我们使用配对的多传感器数据,通过多维上下文中的跨传感器重建训练来提取特征。这一复杂的过程不仅有利于跨传感器特征融合,而且有效地缩小了现有的特征差距。此外,为了在微调阶段获得更多的判别表示,我们引入了显著性模块。该模块通过加减运算,注入人类的先验知识,放大了两种模态之间的差异。这种在共享空间中逐渐扩大正常和异常数据特征之间的距离,使得类内表示更加紧凑,有效地增强了边缘特征的分类。
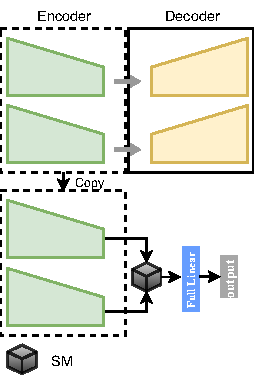
图1 网络整体框图
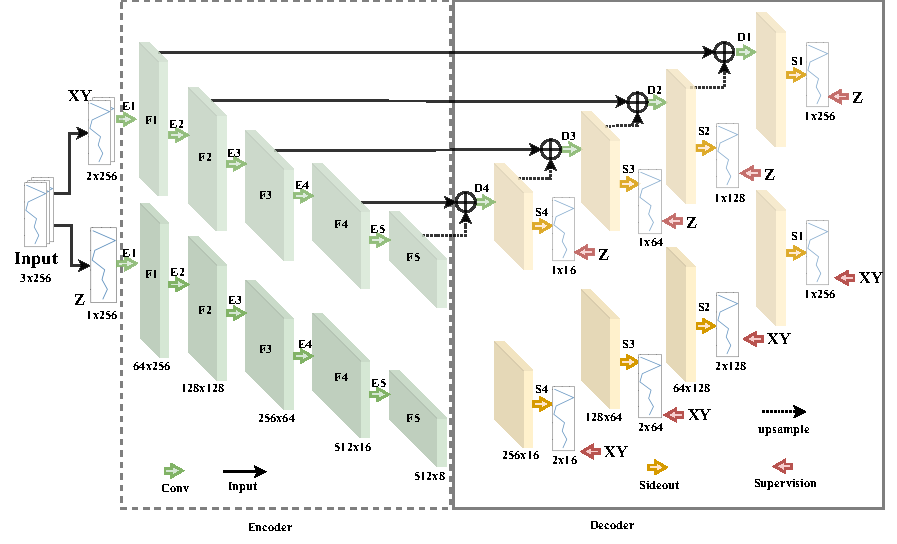
图2 预训练网络框图
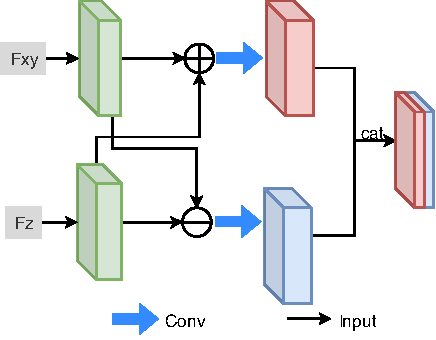
图3 Salience 模块
本文主要贡献可总结为三点:
-
一设计了一种新的两阶段生成式自监督故障检测框架。具体来说,我们引入了一个涉及多维方式的跨传感器重建的预训练借口任务。这种方法通过利用大量未标记的数据来增强判别任务。
-
一提出了一种显著性模块,在微调阶段放大提取特征的可分辨性,注入人为先验,提高边缘特征的差分显著性。
-
一在SMT减震器数据集和FEMTO-ST数据集上的实验结果均优于最先进的故障检测算法。
实验结果
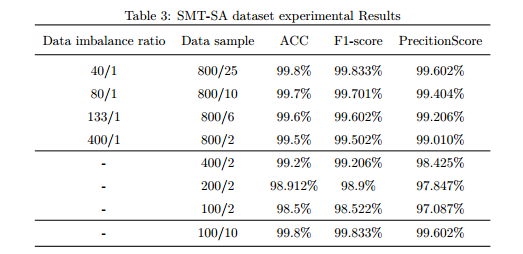
图4 实验结果表
考虑到工业场景中正样本量远大于负样本量,初始正样本量和负样本量分别设置为800个正样本和25个负样本,并逐步减少带标签的负样本量。在这种情况下,模型仍然保持稳定的性能,这符合模型的设计思想。最后,通过最后一行实验数据,表明该模型在极少量的标记数据下仍然可以得到令人满意的结果。
图4显示了SVM预测结果作为混淆矩阵的可视化。验证了该方法的优良性能。图5为不同不良品权重下的模型性能对比。可以看出,虽然增加缺陷产品的权重会慢慢提高召回率,但也会造成准确率的显著下降。这表明,增加缺陷权重会导致模型简单地将更多的好产品预测为缺陷,从而导致F1分数逐渐下降,而F1分数是模型整体性能的一个指标。
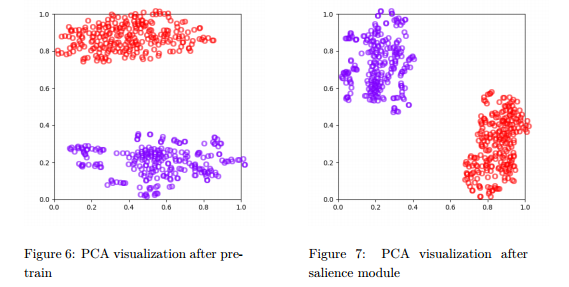
图5 特征可视化
将预训练的特征与显著性模块后的特征进行视觉对比,如图6和图7所示。其中红色点表示正常数据,紫色点表示异常数据。从图中可以看出,预训练的特征已经被准确地分成了类。SM后的特征情况与预期一致,类内特征聚类较多,类间特征聚类范围较大。虽然经过预训练的数据已经获得了很好的分类结果,但是在此基础上引入显著性模块,增加了模型在极端条件下的稳定性。
参考文献
- [1]“Cross-sensor Generative Self-supervised Learning Network for Fault Detection under Few Samples,” 系统科学与复杂性(英文), 2024.